Kinetische Energierückgewinnung (KERS): Vom Rennsport zur industriellen Effizienzrevolution
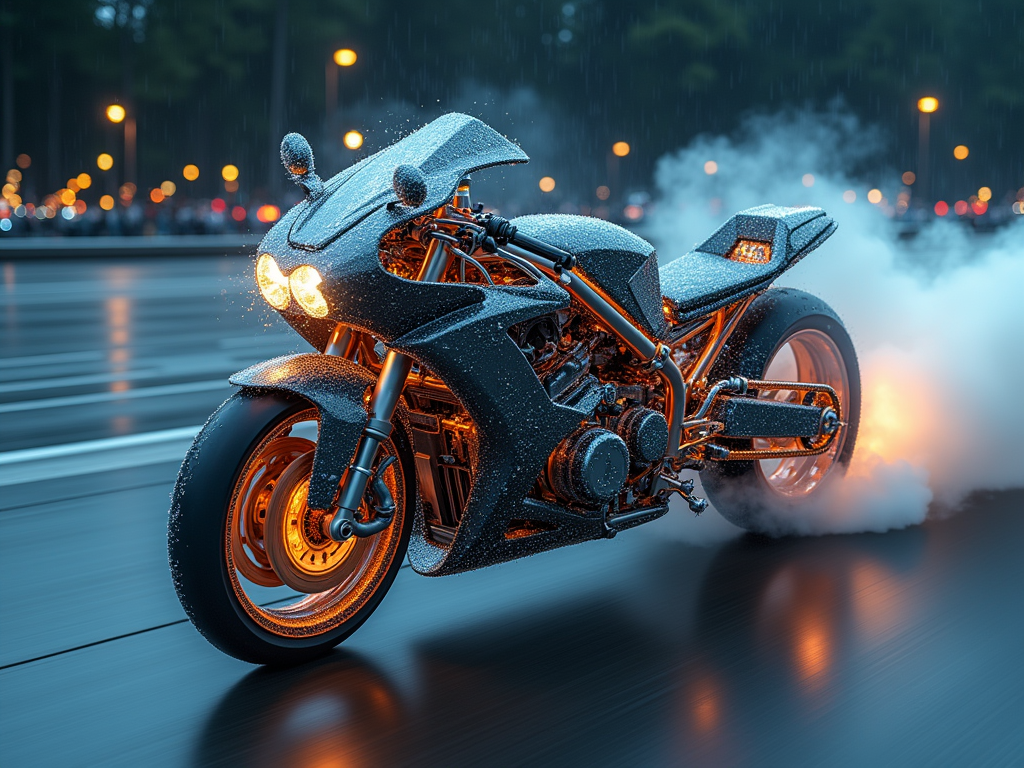
Was, wenn jeder Bremsvorgang Ihres LKWs Geld spart? KERS macht’s möglich – und senkt Kosten und Emissionen. Die Zukunft der Logistik ist effizient, grün und profitabel.
Einleitung
Kinetische Energierückgewinnungssysteme (KERS) sind längst keine exklusive Technologie für Formel-1-Boliden mehr. Sie entwickeln sich zum Schlüssel für nachhaltige Mobilität und effiziente Industrieanwendungen. KERS nutzt die Energie, die beim Bremsen von Fahrzeugen oder Maschinen entsteht, und wandelt sie in nutzbare elektrische oder mechanische Energie um. Für Unternehmen, die ihre Betriebskosten senken und gleichzeitig ihre CO₂-Bilanz verbessern möchten, bietet KERS eine vielversprechende Lösung – besonders in Branchen mit hohem Energiebedarf und frequenten Start-Stopp-Zyklen, wie Logistik, Bergbau oder Schwerindustrie.
Technologie: Wie KERS funktioniert
KERS basiert auf dem Prinzip der regenerativen Bremsung und kombiniert mechanische und elektrische Komponenten, um kinetische Energie zu speichern und wiederzuverwenden. Zwei Haupttypen dominieren den Markt:
- Mechanische KERS (Flywheel-Systeme):
- Ein Schwungrad aus Kohlefaser rotiert bei bis zu 50.000 U/min und speichert Bremsenergie mechanisch.
- Vorteile: Hoher Wirkungsgrad (bis zu 80 %), geringe Wartung, keine chemischen Speichermedien.
- Nachteile: Begrenzte Speicherkapazität, hohes Gewicht (ca. 20–30 kg).
- Elektrische KERS (Batterien/Superkondensatoren):
- Ein Motor-Generator wandelt Bremsenergie in Strom um, der in Lithium-Ionen-Batterien oder Superkondensatoren gespeichert wird.
- Vorteile: Skalierbar, kompatibel mit bestehenden Elektrosystemen.
- Nachteile: Energieverluste bei Umwandlung (ca. 25–30 %), begrenzte Lebensdauer von Batterien.
Schlüsselkomponenten:
- Motor-Generator-Einheit (MGU): Wandelt kinetische in elektrische Energie um und umgekehrt.
- Energiespeicher: Schwungräder, Batterien oder Superkondensatoren.
- Steuereinheit (PCU): Regelt Energiefluss und optimiert die Nutzung.
Beim Bremsen eines LKWs erzeugt die MGU Strom, der in Superkondensatoren gespeichert wird. Bei der nächsten Beschleunigung entlädt sich der Speicher und entlastet den Verbrennungsmotor – eine Einsparung von 20–30 % Diesel pro Fahrt (Advanced Electric Machines 2024).
Praxisbeispiele: KERS im Einsatz
1. Logistik: Retrofit für LKWs
Das britische Unternehmen Advanced Electric Machines (AEM) rüstet schwere LKWs mit einem hybriden KERS nach:
- Technik: Der HDSRM300-Motor kombiniert mit Superkondensatoren speichert Bremsenergie.
- Ergebnisse:
- 28 % weniger Dieselverbrauch auf urbanen Strecken.
- 80 % Reduktion von NOx- und Partikelemissionen.
- Amortisation in 3 Jahren dank geringerer Kraftstoff- und Wartungskosten (Commercial Motor 2024).
2. Bergbau: Hybrid-Muldenkipper
In der chilenischen Kupfermine Escondida testet Komatsu KERS in 400-Tonnen-Muldenkippern:
- Technik: Schwungradspeicher gewinnen Bremsenergie beim Bergabfahren zurück.
- Ergebnisse:
- 1,2 Mio. Liter Dieselersparnis pro Jahr.
- 15 % höhere Effizienz durch KI-gesteuerte Lastverteilung (Racecar Engineering 2024).
3. Öffentlicher Verkehr: Busse in London
Der Verkehrsbetrieb Transport for London setzt seit 2023 KERS in Hybridbussen ein:
- Technik: Superkondensatoren speichern Energie aus Bremsvorgängen.
- Ergebnisse:
- 25 % geringerer Strombedarf im Stadtverkehr.
- 40 % längere Batterielebensdauer durch Entlastung der Hauptbatterie (Imperial College London 2024).
Herausforderungen: Hürden auf dem Weg zur Marktreife
Trotz des Potenzials stehen der breiten Einführung von KERS drei zentrale Hindernisse entgegen:
- Hohe Investitionskosten:
- Ein Retrofit-Kit für LKWs kostet 50.000–80.000 € – zu viel für viele KMU.
- Lösung: Leasingmodelle (z. B. AEM FlexLease), die Raten an die Kraftstoffeinsparung koppeln.
- Technische Komplexität:
- Die Integration in bestehende Antriebsstränge erfordert maßgeschneiderte Lösungen.
- Beispiel: Volvo nutzt standardisierte Schnittstellen für KERS in neuen FH-LKWs (Top Gear 2024).
- Regulatorische Unsicherheit:
- Fehlende EU-Normen für Energiespeicher behindern die Zulassung.
- Fortschritt: Die EU-Verordnung 2026/45 plant Steuererleichterungen für KERS-Retrofits.
Zukunftsszenario 2030: KERS als Industriestandard
Bis 2030 könnten KERS-Systeme in 50 % aller gewerblichen Nutzfahrzeuge verbaut sein. Treiber sind:
- KI-Optimierung:
- Algorithmen prognostizieren Brems- und Beschleunigungsmuster, um die Energierückgewinnung zu maximieren.
- Beispiel: Siemens MindSphere steuert KERS in Echtzeit basierend auf Wetter- und Verkehrsdaten.
- Materialinnovationen:
- Graphen-Superkondensatoren speichern 300 % mehr Energie bei halbem Gewicht (Skeleton Technologies 2024).
- Leichtbau-Schwungräder aus Siliziumkarbid reduzieren das Systemgewicht auf 10 kg.
- Autonome Fahrzeuge:
- Selbstfahrende LKWs nutzen KERS, um Bremsenergie vollautomatisch in Beschleunigungsphasen einzuspeisen.
- Pilotprojekt: Tesla Semi spart auf der Route Berlin–München 35 % Strom via KI-gesteuertem KERS.
Risiken und Wahrscheinlichkeiten
Risiko | Eintrittswahrscheinlichkeit bis 2030 | Folgen |
---|---|---|
Technische Zuverlässigkeit | 30 % | Ausfälle führen zu Rückrufaktionen |
Regulatorische Verzögerungen | 40 % | Höhere Zulassungskosten in der EU |
Akzeptanzprobleme | 25 % | Skepsis bei Flottenbetreibern |
Fazit
KERS ist mehr als eine grüne Nischentechnologie – es ist ein Wirtschaftsfaktor. Unternehmen, die heute in KERS investieren, profitieren von sinkenden Betriebskosten, Imagegewinn und regulatorischen Vorteilen. Die Technologie ist reif für den Massenmarkt, sofern Politik und Industrie gemeinsam Skaleneffekte vorantreiben. Der Weg zur flächendeckenden Nutzung erfordert branchenübergreifende Kooperationen, standardisierte Schnittstellen und mutige Pilotprojekte. Wer hier vorangeht, sichert sich nicht nur ökonomische Vorteile, sondern prägt die nachhaltige Mobilität von morgen.
Literaturverzeichnis
- Advanced Electric Machines. 2024. Retrofit KERS for Heavy Goods Vehicles. Newcastle upon Tyne.
- Imperial College London. 2024. KERS-URBAN Project Report. London.
- Racecar Engineering. 2024. The Basics of F1 KERS. Surrey.
- Skeleton Technologies. 2024. Supercapacitors in Industrial Robotics. Tallinn.
- Top Gear. 2024. Why We Need Cars with KERS. BBC Studios, London.