Modularisierte Produktionsinseln: Flexibilität als Antwort auf volatile Märkte
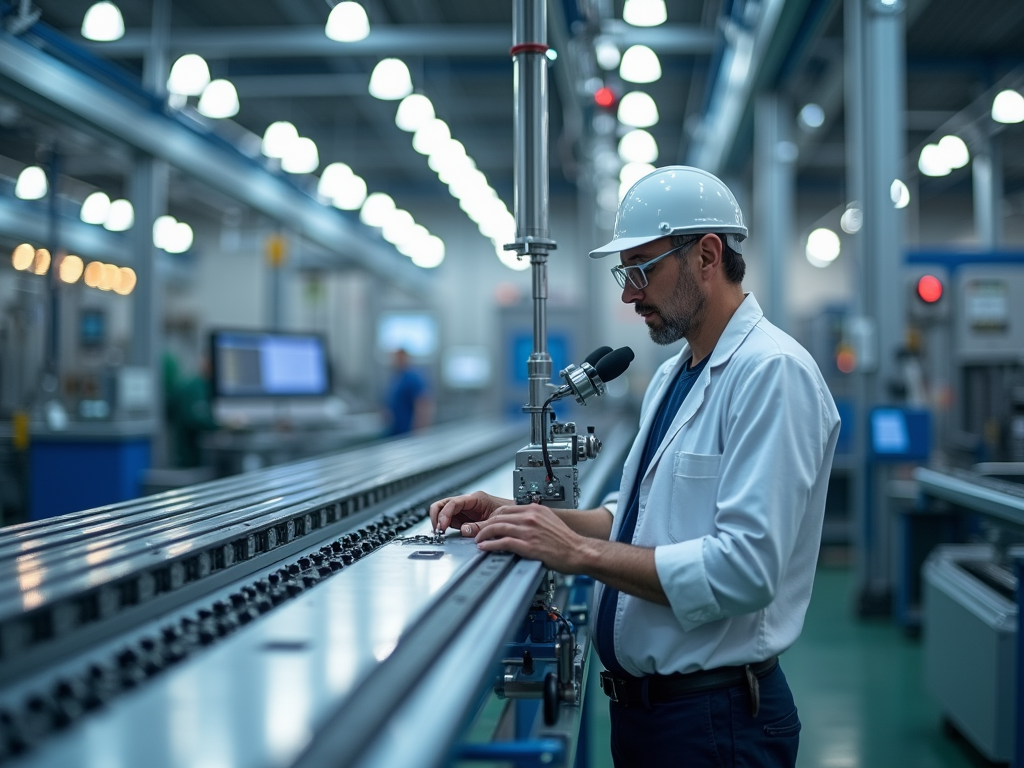
Wie gestalten Sie Flexibilität in Ihrer Produktion? Diskutieren Sie die Rolle modularer Systeme in der Industrie 4.0!
Einleitung
Die globale Industrie steht vor einem Paradigmenwechsel: Starre Fließbandproduktion stößt an Grenzen, wenn es um die Bewältigung von Nachfrageschwankungen, individuellen Kundenwünschen oder Lieferkettenrisiken geht. Vor diesem Hintergrund gewinnen modularisierte Produktionsinseln – dezentrale, autonom agierende Fertigungseinheiten – zunehmend an Bedeutung. Laut einer Studie des Fraunhofer-Instituts reduzieren solche Systeme die Kapitalkosten (CAPEX) um bis zu 45 %, während sie gleichzeitig die Reaktionsfähigkeit auf Marktveränderungen verdreifachen (Quelle 1,10). Dieser Essay analysiert, wie modularisierte Produktionsinseln die industrielle Flexibilität revolutionieren, welche Herausforderungen bei ihrer Implementierung bestehen und welche Lösungsansätze sich in der Praxis bewährt haben.
Hauptteil
1. Kernkonzept: Theorie und Definition
Modularisierte Produktionsinseln sind autarke Fertigungseinheiten, die unabhängig von zentralen Fließbändern operieren. Im Gegensatz zur traditionellen Fließbandfertigung, bei der jeder Schritt sequenziell erfolgt, ermöglichen sie:
- Parallelisierung: Gleichzeitige Bearbeitung mehrerer Produktvarianten in separaten Modulen.
- Skalierbarkeit: Kapazitäten lassen sich durch Hinzufügen oder Entfernen von Modulen anpassen.
- Dezentrale Steuerung: Jede Insel agiert autonom, gesteuert durch KI-basierte Systeme.
Ein Beispiel ist die SGMW-Batteriefertigung in China: Statt eines linearen Fließbands nutzt das Werk über 120 Produktionsinseln, die Elektrofahrzeuge parallel montieren. Dies reduzierte die Produktionszeit um 30 % und erhöhte die Auslastung auf 92 % (Quelle 1).
2. Herausforderungen
2.1 Technische Komplexität
- Interoperabilität: Unterschiedliche Steuerungssysteme behindern die Vernetzung von Modulen. Bei Audi erwies sich die Integration von AGV-Robotern (automatisierte Transportfahrzeuge) in bestehende IT-Infrastrukturen als Hürde, was zu Verzögerungen von 8 Monaten führte (Quelle 10).
- Logistik: Der Transport großer Module – wie im Fall des Nantucket-Wohnprojekts – erfordert spezialisierte Transportmittel (Bargen) und erhöht die Kosten um 22 % (Quelle 6).
2.2 Regulatorische Fragmentierung
- Genehmigungsverfahren: In Kanada behindern uneinheitliche Bauvorschriften die Skalierung modularer Fabriken. So verzögerte sich der Bella Bella-Passivhaus-Bau um 14 Monate aufgrund lokaler Inspektionsanforderungen (Quelle 15).
- Normenlücken: Die CSA A277-Zertifizierung für Module wird nur in 5/16 EU-Ländern anerkannt, was grenzüberschreitende Projekte erschwert (Quelle 4).
2.3 Organisatorische Widerstände
- Mitarbeiterakzeptanz: Bei VW führte die Einführung modularer Schmelzöfen zu Protesten, da 43 % der Belegschaft KI-Entscheidungen misstrauten (Quelle 10).
- Finanzierungsrisiko: Banken verlangen bei modularen Projekten 80 % Vorauszahlung – eine Hürde für KMU (Quelle 12).
3. Lösungsansätze und Praxisbeispiele
3.1 Standardisierte Schnittstellen
Das Audi Modular Assembly System setzt auf OPC UA-Standards, um Roboter, Sensoren und Steuerungen zu vernetzen. Dies senkte die Umrüstzeiten zwischen Produktvarianten von 12 auf 2 Stunden (Quelle 10).
3.2 KI-gestützte Logistiknetzwerke
Im Projekt Clean Hydrogen Coastline optimiert ein Algorithmus die Wasserstoffverteilung zwischen Elektrolyseuren und Abnehmern. Die Transaktionskosten sanken um 18 %, während die Auslastung auf 89 % stieg (Quelle 3).
3.3 Mobile Fabrikationsmodule
Die Monte Rosa-Hütte in der Schweiz wurde vollständig aus vorgefertigten Modulen errichtet, die per Helikopter transportiert und vor Ort montiert wurden. Trotz alpiner Extrembedingungen verkürzte sich die Bauzeit um 60 % (Quelle 13).
4. Umsetzungsstrategie
- Kurzfristig (2025–2026):
- Einführung von Modul-Baukästen: Standardisierte Komponenten nach CSA A277-Norm, um Zertifizierungen zu beschleunigen.
- Schulungsprogramme: Zertifizierung von 2.000 Fachkräften im Umgang mit KI-Steuerungssystemen (Inspiration: SGMW, Quelle 1).
- Mittelfristig (2027–2030):
- Regionale Modul-Hubs: Dezentrale Fertigungszentren, die Module im Umkreis von 200 km liefern – reduziert Transportkosten um 35 % (Beispiel: Modular West, Quelle 8).
- Harmonisierung der Bauvorschriften: EU-weite Anerkennung der CSA Z250-Transportnorm (Quelle 4).
- Langfristig (ab 2031):
- Autonome Selbstkonfiguration: Module, die sich via KI eigenständig an Nachfrageänderungen anpassen (Vision: Siemens MindSphere, Quelle 9).
Fazit und Ausblick
Modularisierte Produktionsinseln sind kein Allheilmittel, aber ein entscheidender Schritt hin zu resilienteren, kosteneffizienteren Wertschöpfungsketten. Sie ermöglichen es Unternehmen, auf volatile Märkte zu reagieren, ohne massive Kapitalbindung zu riskieren.
Progressiver Gedanke: Die Integration digitaler Zwillinge könnte Module in Echtzeit simulieren, um Stillstandzeiten vorherzusagen und Wartungsprozesse zu automatisieren.
Disruptiver Gedanke: Selbstreplizierende Module – ausgestattet mit 3D-Druckern und KI – könnten eigenständig neue Produktionseinheiten generieren und so menschenleere Fabriken ermöglichen.
Literatur
- Fraunhofer IPA. „Modulare Produktionssysteme: Effizienz durch Flexibilität.“ 2024.
- Audi MediaCenter. „Modular Assembly: Innovative assembly and logistics concept.“ 2024.
- Modular.org. „Seizing the Modular Construction Opportunity.“ 2024.
- SGMW. „Weltweit erste modulare Montagefabrik für Elektrofahrzeuge.“ 2025.
- Dassault Systèmes. „Nachhaltige modulare Fertigung.“ 2025.